3D принтеры заменят токарные станки
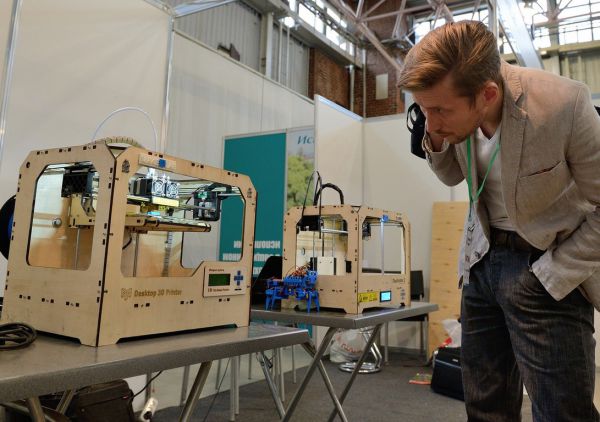
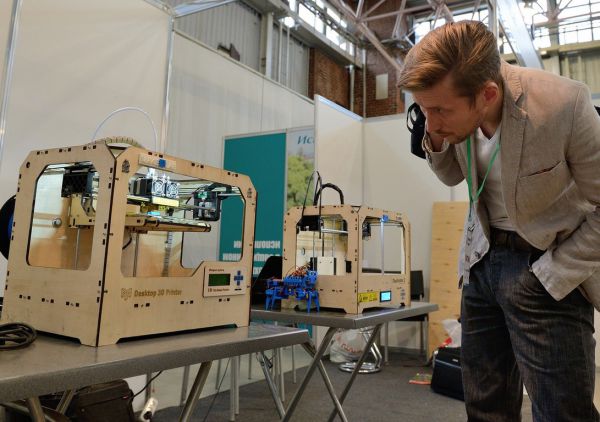
За рубежом аддитивные технологии уже используют достаточно широко: на принтерах печатают элементы оснастки, искусственные органы, декор, модели архитектурных объектов, колодки сложной формы для обуви и т. п.
В России этот процесс только начинается. Есть мнение, что аддитивные технологии могут решать только узкий круг задач, связанных с прототипированием, моделированием, мелкосерийным производством. Но, как показало обсуждение этой темы на круглом столе, прошедшем в рамках Иннопрома, организовали который кластер космических технологий и телекоммуникаций фонда «Сколково» и свердловская «Титановая долина», это далеко не так.
Наиболее активно в процесс разработки и внедрения аддитивных технологий вовлечена аэрокосмическая отрасль. Как отметил генеральный директор холдинга «Технодинамика» Максим Кузюк, в российской авиационной промышленности уже используется восемь аддитивных технологий. Применяют их и на «Технодинамике», хотя и не очень широко. Накопленный предприятием опыт показал, что эти технологии позволяют повысить конкурентоспособность продукции, существенно снизить сроки проектирования, себестоимость. Скорость изготовления деталей увеличивается в 20 раз, для этого не требуется изготавливать оснастку. На одном оборудовании (принтере) можно делать разные детали, причем разных конфигураций и из разных материалов, что невозможно при существующих способах обработки. В 20—50 раз сокращается время на реинжиниринг изделия, а такая необходимость возникает нередко при освоении новой продукции, в два раза уменьшаются энергозатраты. И главное — экономятся материалы, которые постоянно дорожают: расход материалов уменьшается в три раза. В результате предприятие рассчитывает снизить затраты на производство одной детали вдвое.
Достаточно активно внедряют аддитивные технологии в компаниях «Боинг» в России и СНГ, Росатоме, ВСМПО-АВИСМА, где разрабатывают новые виды порошков, которые могут использоваться при 3D печати, НПО «Сатурн». Но, по ряду причин, широкого прорыва на российском технологическом фронте пока не произошло, несмотря на все преимущества аддитивных технологий.
Что это за причины? Максим Кузюк одной из главных преград считает то, что эти технологии можно применять лишь при изготовлении новых изделий. Но все, что у нас сегодня производится, — старые разработки. Генеральный директор АО «Наука и инновации» Росатома Алексей Дуб отметил, что не каждый конструктор возьмет на себя ответственность за применение инновационной технологии. Для того чтобы в этом деле у нас произошел прорыв, необходим комплексный подход: нужно иметь материалы, которые используются при 3D печати, собственные новые конструкции, оборудование, на котором эти изделия будут изготавливаться.
Оборудование многие компании уже закупили. В частности, в УрФУ создан центр аддитивных технологий, есть 3D принтер, которым смогут пользоваться разработчики, чтобы проверить, будет их новое изделие работать или нет. Разработки тоже начинают появляться, в том же Всероссийском научно-исследовательском институте авиационных материалов таким способом уже изготовлено 120 деталей для трех новых авиационных двигателей. Но вот серийного производства порошков для печати, в том числе титановых, в России пока нет. Как отметил президент компании «Боинг» в РФ Сергей Кравченко, титан сегодня второй материал после композитов, применяемый в авиастроении. Уральское ВСМПО-АВИСМА титан производит, но мало. Большая его часть идет на детали для авиации. В настоящее время здесь оценивают технологии по производству титановых порошков, работают с рядом предприятий, производящих оборудование для производства порошков.
Но главным препятствием на пути применения аддитивных технологий в серьезных отраслях российской промышленности является отсутствие стандартов и сертификации продукции. «Боинг» такие детали сертифицирует в США. Другие компании также получают сертификаты за рубежом. А это очень дорогое удовольствие — сертификация одного материала обходится в 4 млн евро. Как пояснил исполнительный директор кластера космических технологий и телекоммуникации фонда «Сколково» Алексей Беляков, российских стандартов пока нет, их надо разрабатывать. Власти ждут, когда появится продукт, который нужно будет сертифицировать, испытывать. Позиция такая: пускай промышленность сначала сформирует заказ, производители сделают продукт. Но от нашей промышленности еще нет запроса на такую продукцию, поэтому сертифицировать нечего. Пока не будет сформулирован запрос, не будет соответствующего предложения, о сертификации говорить бессмысленно.
Заместитель директора департамента металлургии и тяжелого машиностроения Минпромторга РФ Михаил Иванов отметил, что работа по выработке стандартов уже началась. Но успешное развитие отрасли должно осуществляться путем объединения производственных, научно-технических и коммерческих сил. Для этого необходимо сформировать единую научно-техническую политику, которая будет координировать процессы создания и внедрения этой технологии в различных отраслях промышленности. Минпромторг уже дал команду на разработку подпрограммы по производству оборудования, в нее войдут робототехника, аддитивные и цифровые технологии. Важно также работать в единой цепочке: производить материалы, оборудование, разрабатывать и изготавливать конечный продукт. Немаловажно знать, есть ли спрос на эту продукцию, какие требования к ней предъявляют заказчики, какое качество их устроит.